System Structure | - Aerosol Generation: 1.7 MHz Ultrasonic Enhanced Bubbler can "evaporate" catalyst liquid with literally no heat generated. A stainless steel liquid collector connects inline with the ultrasonic bubble can prevent condensing liquid from streaming into the furnace tube chamber.
- Thermal Decomposition: three-zone ( 900mm length ) tube furnace can be heated up to 1200C maximum to pass the droplets flux across the temperature and atmosphere regulated firing zone, chemical, and physical conversion processes proceed.
- Nanopowder Collection: 30KV electrostatic precipitator (700 ml ) can effectively collect nano-size particles from the carrier gas flow
- The furnace can be tilted to avoid liquid flow back atomizing tank
|
Tube Furnace - Thermal Decomposition | Voltage & Power | - Single Phase, 208V~240V AC, 50/60 Hz (30A breaker required)
- Max. 7 KW
|
Working Temperature | - 1100oC continuous
- 1200 oC Max. < 1 hours
|
Max. Heating / Cooling Rate | < 20oC / min |
Heating Zone & Constant Temperature Zone | - Three heating zone, 300+ 300 + 300 mm ( 900mm L total)
- Constant temperature zone: 600 mm with +/- 2oC ( if 3 zone at same )
|
Heating Elements | - Fe-Cr-Al Alloy doped by Mo
|
Temperature Controller 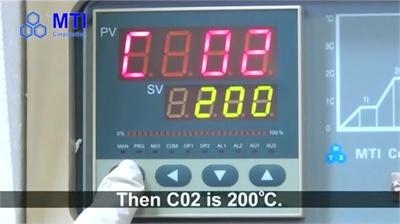 | - Three digital temperature controllers with 30 programmable segments for precise control of heating rate, cooling rate and dwell time.
- Built-in over-temperature alarm and protection allow for operation
- +/- 1 ºC temperature accuracy.
- RS485 Communication Port.
- Precision Eurothermo controller is available with +/- 0.1 oC accuracy
|
Processing Tube | - One fused quartz tube is included with ID 20.5 x OD 25 mm x L 1400 ( mm)
|
Sealing Flanges & Fittings | |
Aerosol Generation  | Ultrasonic atomizing bubbler   | - 220VAC, 1.7 MHz Ultrasonic Generator
- Ultrasonic power is adjustable with 8 levels
- 316 Stainless Steel liquid container with a fluoropolymer sealing ring
- The continuous or timed mode can be set. For timed mode, time can be adjusted from 30 minutes to 180 minutes.
- A liquid injection pump is equipped with a 60 ml plastic syringe. The speed range for the liquid injection pump is 0.004 ml/min - 70 ml/min
- A floating flow meter is included to control the carrier gas flow rate within 0-200 SCCM.
- A mass flow controller (MFC) is optional to precisely control the flow rate.
|
Nanopowder Collection  | High Voltage Supply  | - AC 220V 50/60Hz, 30 W Max. power consumption
- Digital Voltmeter and Current meter, 30KV, 1.0 mA max.
- Output voltage and current can be set by using knobs on the front panel and read from the digital display
- Built-in Arc Protection Circuit
|
Electrostatic Precipitator | - KF25 quick clamp and flange enables the quick coupling to the furnace processing tube
- 1/4" gas outlet built-in
- Another KF25 port is built-in with the collector to connect the vacuum pump, which is required, but not included
- PEFE plates are installed on top and bottom to insulate high voltage electrodes
- Adjustable supports keep the collector leveled with the furnace tub
|
Net Weight | ~150Kg |
Dimensions | ( click the picture to see details) |
Warranty | One-year limited manufacturer warranty with lifetime support (consumable parts such as furnace liner, processing tubes, and O-rings are not covered by the warranty, please order replacements at related products below). |
Laptop, software & WiFi Control (Optional)  | - Brand new laptop with Microsoft Windows 10 and Microsoft Office 2013
- Labview Based Temperature Control System (EQ-MTS01) enables the user to edit temperature profiles, manage heat-treatment recipes, record and plot data for MTI furnaces.
|
Compliance | - CE Certified
- NRTL or CSA certification (UL61010) is available upon request at extra
|
Application Notes   | - A two-stage pressure regulator must be installed on the gas cylinder to limit the pressure to below 3 PSI for safe operation. Click here to learn the installation of a gas regulator.
- Please tilt furnace in 10 - 15 degrees to avoid liquid back to atomizing bubbler
- It is the customer's responsibility to achieve the ideal parameter for particle size. Usually, the liquid injection rate and carrier gas flow rate has an important influence on particle size.
- The SEM picture left is SnO2 particle ( ~ 500 nm - 5 um) generated by the equipment via Stannic chloride solution at 800oC
|
Operation Video & Instructions |  |