Power | - Wire Saw Control Consol: Universal 110V or 240VAC, 50/60Hz, 200W max.
|
Structure
 | - Heavy-duty aluminum alloy structure with compact size
- automatically controlled Y-axis by the digital panel
- single wire swing cutting with adjustable wire length from 5-15mm (broken wire still can be used)
- Transparent plastic plates are included to prevent Coolant splashing
- Add an oil refill cup behind the forming tube, please apply 10-15 drops Anti-Wear Oil before first-time use
- Wire spooler motor, 3 Amps, Torque = 1.8Nm
|
Sample stage
| - Z-axis: 50mm, automatically controlled by the digital panel
- Y-axis: 50mm, automatically controlled by the digital panel
- Two-dimension sample stage built-in 360° degree horizontal rotating and +/-10° tilting vis manual operation
 |
Cutting parameters
 | - Feed Speed: 0.01 mm/min to 40 mm/min adjustable
- Back Speed: 1 mm/min to 100 mm/min adjustable
- Spooler spin speed: 1-260 RPM adjustable
- Cutting depth: 0.1 - 50mm
- Positional accuracy: +/- 0.01 mm
- Please click the picture left to see the samples cut by this machine
|
Meteorite Sample | - Please click the picture below to view the meteorite samples that were cut by our wire saws.
Fig. 2 Fig. 3 Fig. 4 |
Controller & Touch Screen | - Color touchscreen controller will setup wire travel speed, cutting speed and slicing width
 |
Diamond wire | - ≤ 15 meters used for each installation
- One spool of 0.35mm Dia x 20 meters length Diamond Wire is included for immediate use
- A Diamond Blade Dressing Stone is included for keeping the wire sharp
- Optional:
|
Wire tension system
| - Standard: steel spring wire tension system with break wire alarm is included
|
Coolant Pump | - One water pump is included for cooling diamond wire during cutting
- You must use anti-corrosive oil or radiator water as coolant (could buy from any auto store)
- Warning: must clean the machine after each cutting, especially using tap water as the coolant to prevent rust
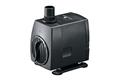 |
Optional | - Swing & Rotation Sample Fixture: Such fixture needs an independent controller for its parameter settings such as swing frequency/ angle (±23°, up to 20 swings/min), rotating speed, and rounds (30rpm max.) Higher cutting surface quality can be expected by swinging or rotating the specimen throughout the cutting process. Please click Pic.2 &3 and video to learn more details. The fixture will enhance cutting speed up to 2 times
Pic.1 Gif.1 Pic.2 Pic.3 Video |
Product dimensions
 | - Saw: 414mm(L) x500mm(W) x750mm(H)
- Controller: 340mm(L) x 290mm(W) x 170mm(H) (click to enlarge the left picture for size detail)
|
Shipping dimensions | 48"(L) x 40"W) x 45" (H) |
Shipping Weight | 220 lbs |
Warranty | One year limited with lifetime support, not including cutting wire |
Certificate | CE certified. With an additional certification fee, MTI can arrange NRTL to perform UL/CSA inspection and label the machine per customer's request. |
Operation Demo Video |  |
Application Notes
 | - The flow rate of the coolant is adjustable by the valve in the blue feeding tubing. Please adjust it properly to improving cutting performance
- Please use the correct cutting fluid. Don't use tap water
- Must clean the machine after each use
- Wire saws applications
- The wire saw can be placed inside the glovebox with N2 gas via feedthrough at an extra cost
|
Warnings | - It is required to use proper cutting fluid with the saw to prevent corrosion of the machine components. We strongly recommend you use an oil-based coolant or lube cool lubricant with the water. Do not use tap water directly, the rust component is not part of the warranty.
- Do not overflush the sample stage, it may rust the Z-axis step motor.
- It is required to apply 10-15 drops Anti-Wear Hydraulic Oil (ISO 32) using an oil can(#19) before first-time use or continue working for 150 hours.
- And a limited amount of grease (general purpose grease will do) should be added to the motor shaft periodically,
- Never cut any materials without the use of proper cutting fluid. If you do so, serious damages can be caused by the spooler driving mechanism.
- For cutting the sticky materials such as non-ferrous alloy, epoxy, and plastic, you must sharpen diamond wire frequently. We suggest that cutting sample along with the included dressing stone (Glue sample and the dressing stone side by side and cut them together, this process will help keep the wire sharp enough for efficient cutting.
- Please clean the machine after the completion of each use.
|